1.はじめに
1.1 概要
組電池やらを作りたいので簡易スポット溶接機を作ってみる。
1.2 必要なエネルギー
対象の最大厚みを1mmとすると溶融スポット径(溶融面積の直径)は1mmくらいないと十分な強度だと感じられない気がするので、目標溶融スポット径を1mmとする。
例えばSUS304の比熱は0.59[J/(g・K)]、密度は7.93[g/cm3]だから、仮に10μm厚みでスポット径1mmを溶融するとすると、62.2μgで27213[K/J]、融点は1400~1450℃だから1600℃くらいにすれば短時間でも溶融するだろうと考えて、1600/27213=0.06J必要な計算になる。
スポット径1mmは対象が0.2mmくらいではやり過ぎ(面積広過ぎ)なので、対象に応じたエネルギーの調整が必要そうである。
ちなみに、例えば銀だと、比熱容量=0.232[J/(g・K)]、密度=10.49[g/cm3]、融点=1235℃だから、エネルギーだけで言えばSUS304が溶かせるエネルギーなら銀も溶かせる。
真鍮も0.377[J/(g・K)]、8.5[g/cm3]、900℃で同様。
1.3 必要なパルス幅
熱拡散長は、(熱拡散長の)比較的小さいステンレスで4mm/1s(12.6μm/10μs)、
比較的大きい銀で26.4mm/1s(83.5μm/10μs)。
熱拡散長は時間の平方根なので、熱拡散長を20μmとするにはステンレスは25μs以下程度だが、銀は0.6μs以下との計算になる。
1.4 流す電流
通常50Vを超えると危険な電圧とされるようだ。今回はコンデンサやFETの耐圧を考慮して35V程度をMAXとしたい。従って、20V,25V,30V,35Vの選択。
仮に5.5mm2のケーブル(3.31Ω/km)で往復1mとして3.31mΩ。
装置内の接続損失など諸々で10mΩとして、ケーブルの合計電圧降下を10Vとすると 1000A。
なので、頑張っても2000~3000A、使いやすい範囲では1000A位が限界な感じである。
仮に負荷(接触抵抗)への実効印加電圧を5Vとして10μs だと1000A5V10μs=0.05J。
SUS304なら丁度良さそうだが、銀の0.6μsは全く無理そうだ。
仮に銀に10μsのパルスを与えると、熱拡散長=83.5μmよりスポット径1mmを溶融するには(比熱容量=0.232[J/(g・K)]、密度=10.49[g/cm3]、融点=1235℃から銀は溶融し易いだろうから融点そのままで計算して)
0.2J必要なので、0.05Jでは不足する。
熱拡散長は時間の平方根、加えるエネルギーは時間比例だから、160μsなら0.8Jで溶融できる計算になる。銀の溶接のときは触れないくらい熱くなるのも止むなしだろう(と言うか、接触状況によっては電極が溶接されるかもしれない)。
1.5 必要なコンデンサー
今回入手できたコンデンサは写真 1 1に示すようなコンデンサ。56000uF 80VでESRを測定したら4mΩだった。かなりイケそうだ。マウスを横に並べてみたけど、かなりでかい!
だからこのコンデンサを使用すると理想的には1msecで112A、100usecで1120Aまで出せることになる。(ちょっと大きすぎたかも・☞)
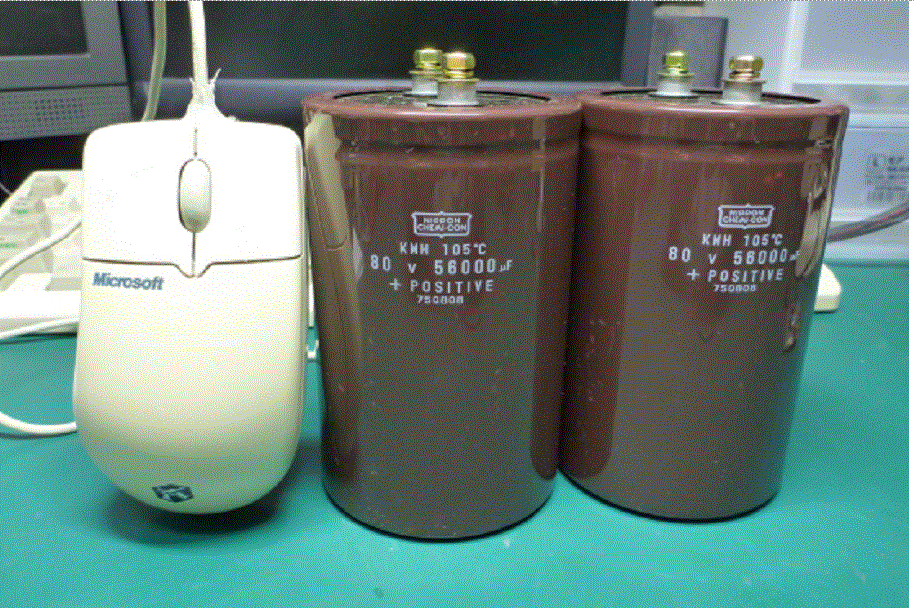
1.6. ニッケルやステンレスがスポット溶接しやすい理由
スポット溶接は、電気抵抗による発熱を利用する溶接です。銅や銀のように電気の良導体よりも、ある程度の電気抵抗がある(電気伝導率が低い)金属のほうが溶接に適しています。
また、溶接する部分の熱が、すぐ逃げてしまう(熱伝導率が高い)ようでは、金属が溶かすことができず溶接は困難です。電気伝導率と熱伝導率は、左の表のように密接に関連しています。
従って、共に適度な値を有する、ニッケルやステンレスは、スポット溶接しやすい金属といえます。 アルミニウムは表面の酸化膜が絶縁体として働くため、溶接時には高電圧をかけてこの酸化膜を破壊する必要があります。 合金の場合は、かなり様子が異なり、銀や銅も合金となったものは、溶接が容易になる場合があります。
金属名W/(m・k)) | 電気伝導率 | 熱伝導率 |
---|---|---|
金 | 45.5 | 320 |
銀 | 61.4 | 420 |
銅 | 59 | 390 |
アルミニウム | 37.4 | 236 |
リン青銅 | 13~15 | 133 |
ニッケル | 14.5 | 113 |
ステンレス | 6~9 | 15~25 |
鉄 | 9.9 | 84 |
電気伝導率(導電率)の高い金属は、熱伝導率(熱伝導度)も高い。つまり、スポット溶接のために電流を流しても発熱が少ない上に熱は逃げやすいので溶接は困難です。それ故にアルミニウムや銅の溶接には、大電力が必要になります。
2.設計
2.1 概略ブロック図
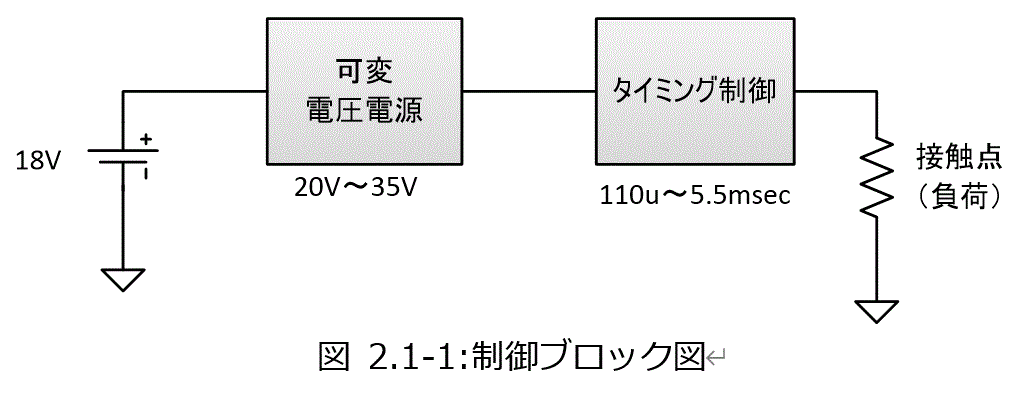
項目 | 仕様内容 |
---|---|
入力電源 | AC100V (内部で18Vの電源として使用する) |
電圧設定範囲 | 20V, 25V, 30V, 35Vから選択 (DC/DCコンバータで18Vから昇圧する) |
パルス設定範囲 | 約110u, 520u,1.1m, 2.4m, 5.5msecから選択 |
出力電流値 | MAX 1000Aくらいかなぁ・・・ |
2.2動作原理
図 2.2 1に制御概略図を示す。動作概要としてはコンデンサに電荷を蓄え、それを一気に放電する方式である。SW1はC1に充電するスイッチで、SW2は放電するスイッチであり、RLは溶接点の等価抵抗を示している。
図 2.2 2にその動作タイミングを示すが、SW1,SW2はそれぞれ排他的な動作となる。またSW2のON時間を可変することで溶接時間を調整する。
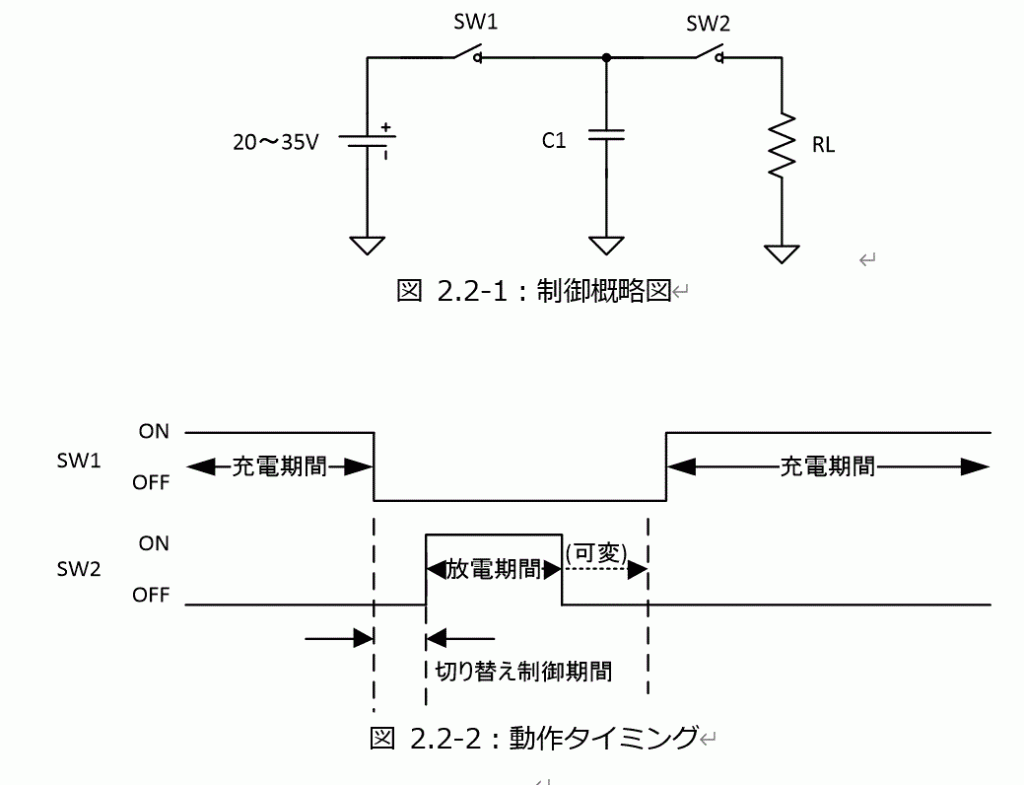
2.3 回路検討(シミュレーション)
2.3.1 シミュレーション回路図
図 2.4 1に主にタイミグ生成回路検討に使用した回路を示す。
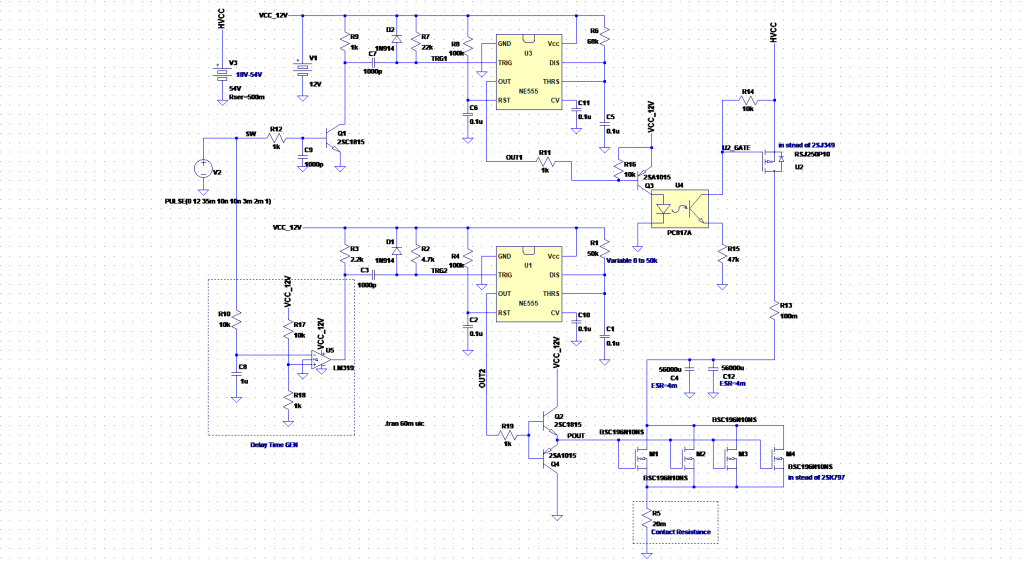
【回路説明】
電源のHVCCは18V~54Vまで可変することを想定。制御部は”VCC_12V”で示すように12V系となっている。これは18Vからレギュレータで作ればいい。V2は外部スイッチを想定しており、フットスイッチなどで、動作ONの時にHIGHとなるような論理となる。タイミング生成はU1,U3のタイマーIC555のワンショットタイマーモードを使用する。U3は充電タイミング用でありU1は溶接電流出力用である。溶接時間(T)は となる。
R1=100Ωとすると約11usecとなる。最大時間はR1=50kΩを想定しているので5.5m程度となるが、コンデンサへの電荷量と負荷R5の関係で有効時間が影響される。回路図の左側にある「Delay Time GEN」は充電制御SWが十分にOFFになってから溶接スイッチをONにするための遅延時間を生成するものである。単純にR10とC8のCR時定数により遅延させているが、そのままの出力を使用すると閾値が小さいので後段のコンパレータU5(LM319)を使用して所定のレベルでタイミング遅延信号を生成している。
タイマーIC555のワンショットタイマモードではTRIGのパルス幅以下に出力幅を小さくすることはできないためC3およびC7でACカップリングしてトリガ成分だけを取り出す。タイミング制約は図 2.4 2の通り。
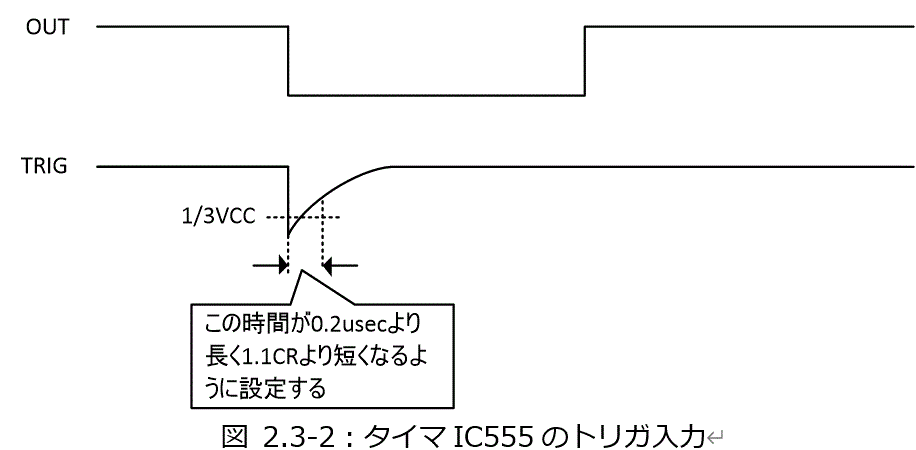
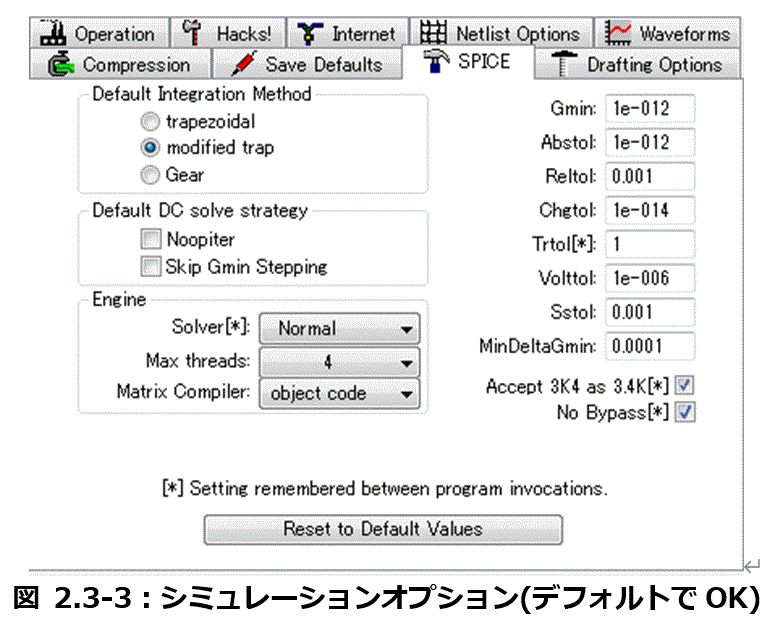
2.3.2 シミュレーション結果
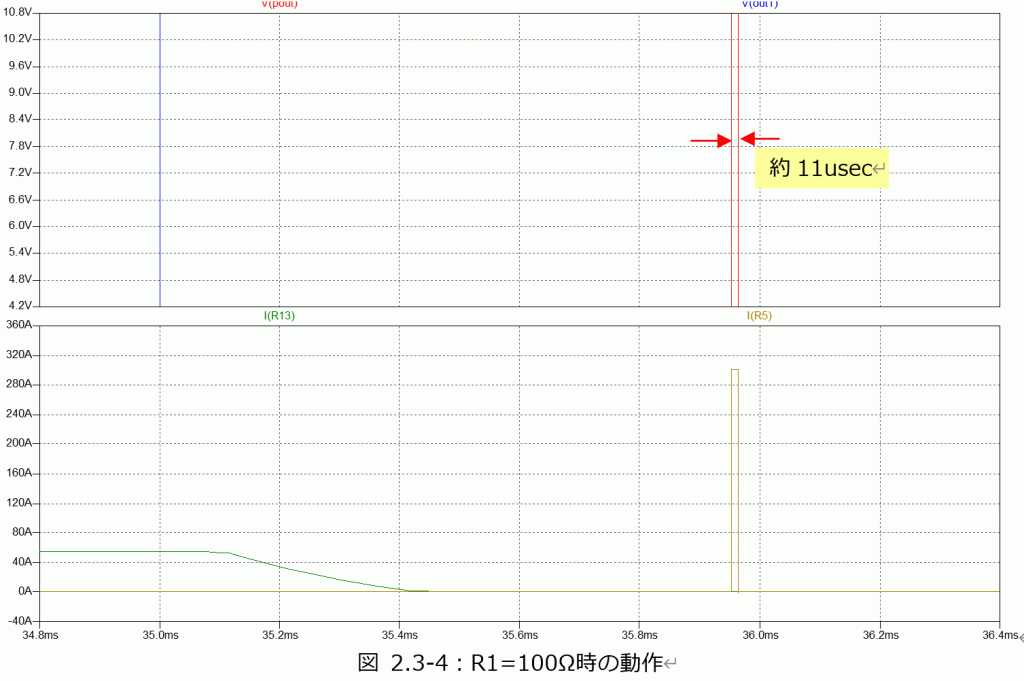
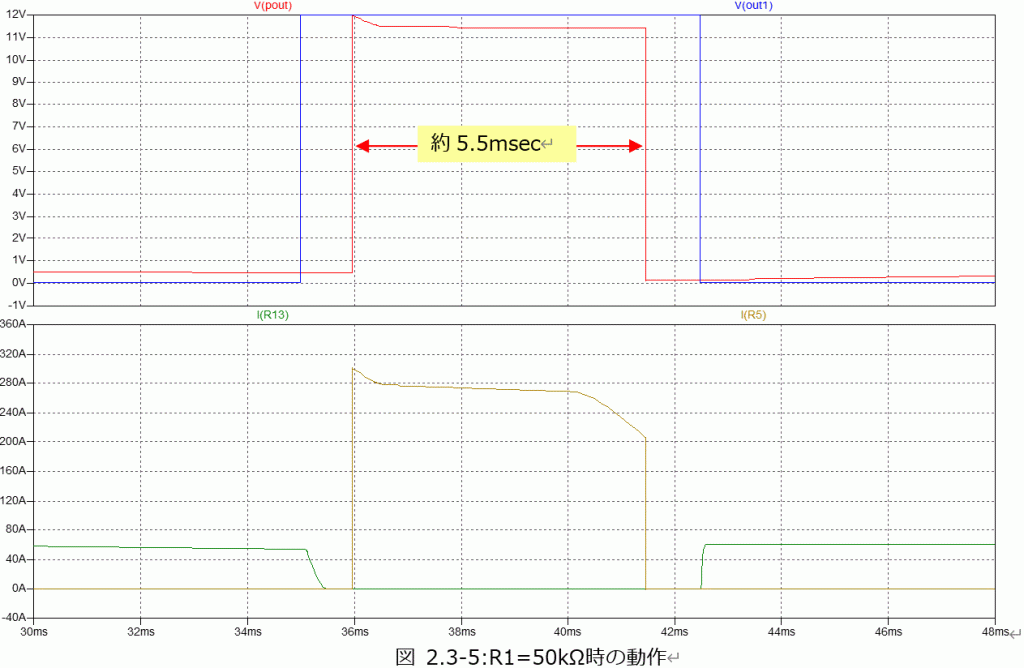
図 2.3 2のI(R3)のグラフからコンデンサの容量が大きすぎて数十msecでは完全に充電しきれていないことが判る。ただ、溶接には十分な電流を得られているのでヨシとこれでいっか!
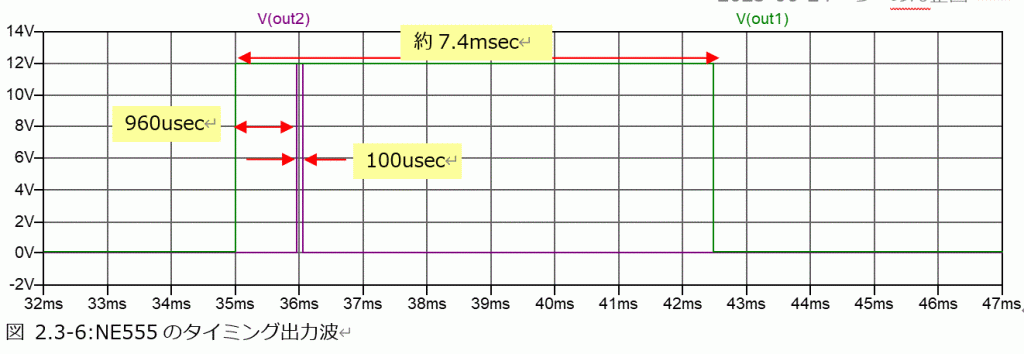
2.4接続図
今回はマイコンを使用せずに単純なアナログ回路のみで構成してみた。
また、電流スイッチのドライブ基板は最初1枚基板で行っていたが、FETを変更したり、メンテしたりする可能性もあるかと思うので別基板とした。
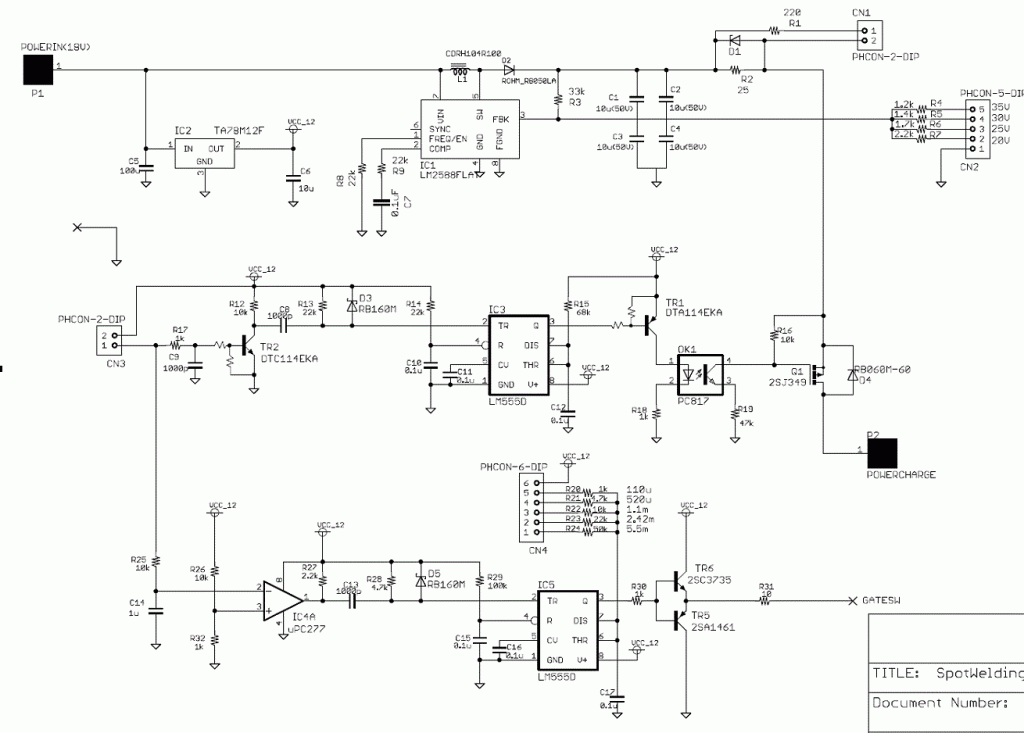
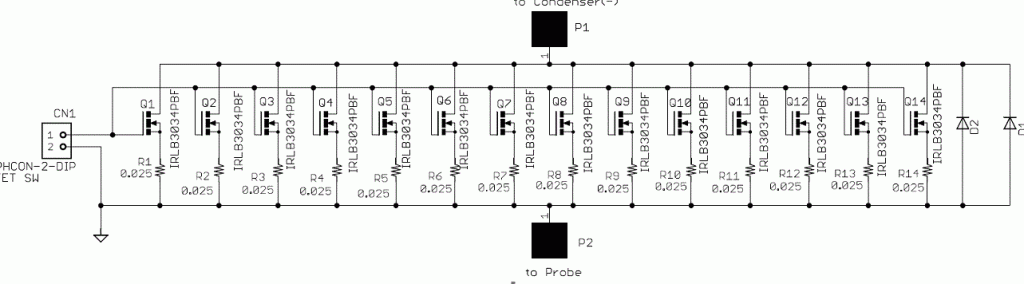
【主な使用部品】
タイミング調整および供給電圧設定基板
部品番号 | メーカー | 仕様・諸元 | 備考 |
---|---|---|---|
U1、U3 | 適当 | タイマーIC 555 | 8pin DIP 今回はバイポーラでもCMOSでもどちらでもいい。 |
U4 | SHARP | PC817A | フォトカプラ |
U2 | TOHSHIBA | 2SJ349 (P-ch MOSFET) | シミュレーションではROHMのRSJ250P10を使用しているがRDS(ON)=33mΩ、VDS=-60V,Vth=-2Vくらいの適当なPch MOSFETであればいいかも。 |
Q1,Q2 | 適当 | 2SC1815 | 相当品でOK |
Q3,Q4 | 適当 | 2SA1015 | 2SC1815とコンプリメンタリのものを使用した。相当品でOKだと思う。 |
U5 | ナショセミ | LM319 | 在庫のコンパレータなので適当なものでOK |
FETドライバーのみ実装した基板
部品番号 | メーカー | 仕様・諸元 | 備考 |
---|---|---|---|
Q1,Q2,Q3,Q4,Q5,Q6,Q7 Q8,Q9,Q10,Q11,Q12 Q13,Q14 | International Rectifier (IOR) | IRLB3034PBF (N-ch MOSFET) | VDssは40Vと低いがON抵抗が1.4mΩと低いため電流を多く流すことができる。連続343Aでパルス次は1372Aである。溶接となると膨大な電流が流れるので、今回これを14個並列につないで1個あたりにかかる電流を分散させている。 (秋月電子通商で購入@250) |
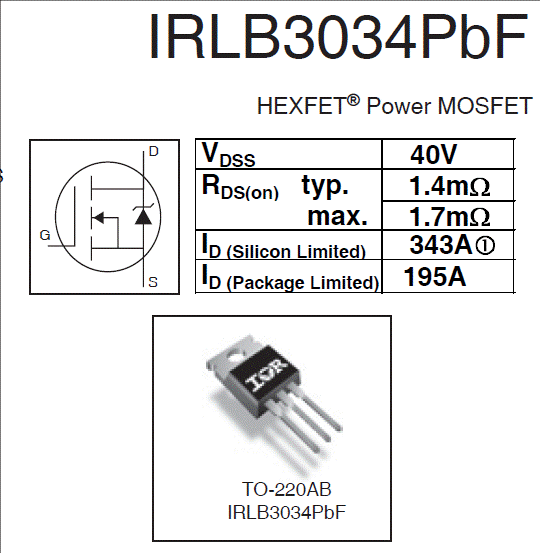
2.5 動作検証(タイミング生成部)
試作基板1を使用してタイミング生成部の動作確認を行った。
タイマIC555の動作はほぼ設計通りの動作することを確認した。
図 4.1 1(これは失敗回路)の接続図のそれぞれタイマIC(IC1,IC3)のタイミグ出力ピン3を測定。
IC3はR10(1KΩ)を接続して100usecの時間に設定
図 2.3 6のシミュレーションとほぼ同じ結果になった。それぞれタイマICで生成されるタイミグ(7.73msec,100usec)はほぼ安定していたがタイマIC間のタイミングはほぼ1.3msecであるが少しばらつきがあるようだ。
2.6 完成写真
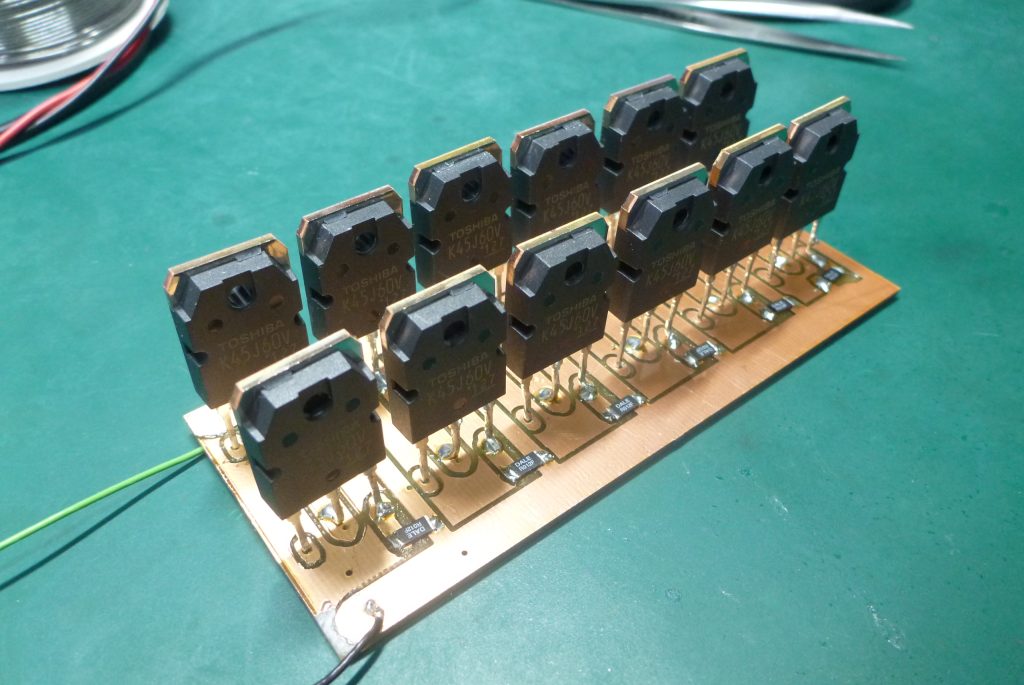
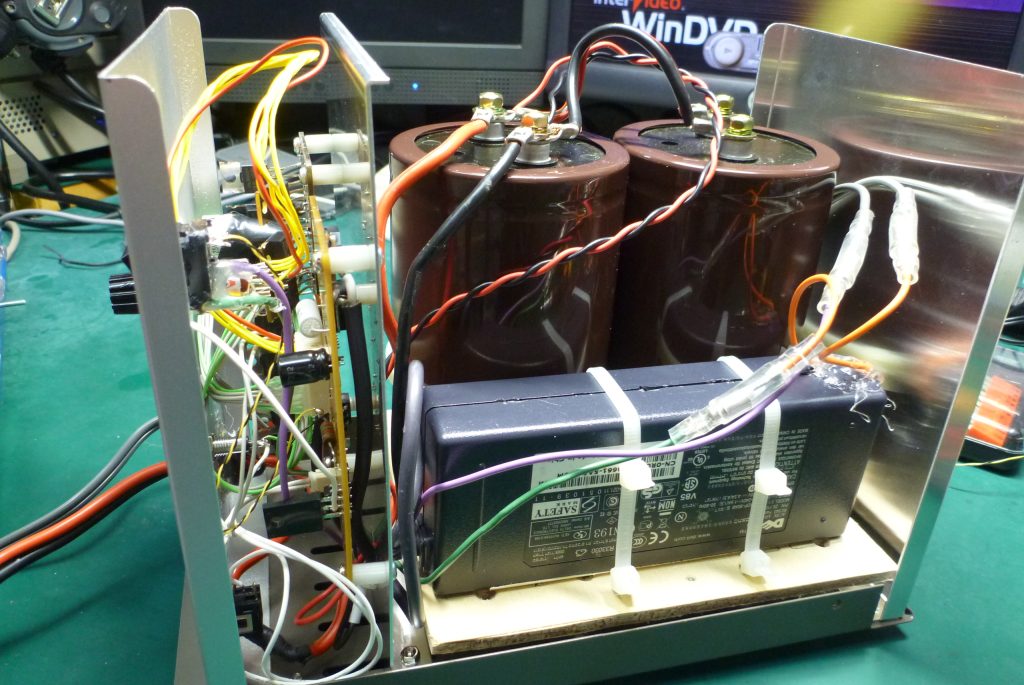
3. 評価試験
3.1 電流制限抵抗R2について
電源20V1.7Aのもので35Vに昇圧する。この時80%の効率とすると0.77Aまでとなる。そこで0.7Aでリミットをかけるとして50Ωの電流制限抵抗を付ける。
(25Vであれば1Aまでいけるので25Ωの抵抗)
チャージ時間はτ=1.1*C*Rより、6sec@50Ω,3sec@25Ωとなる。
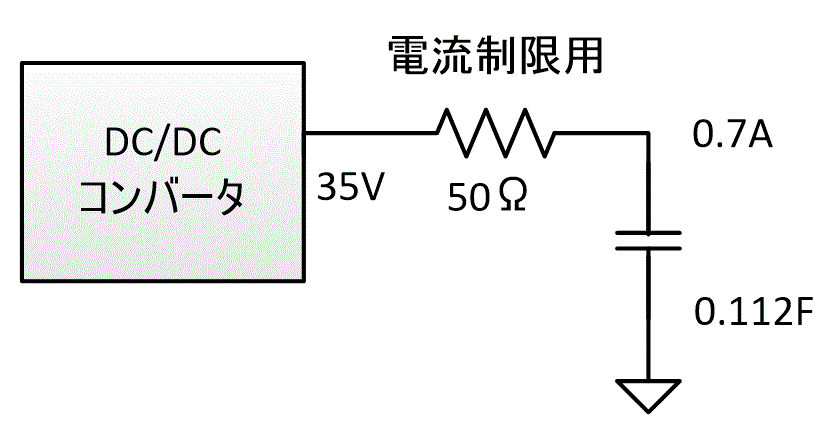
3.2 爆火現象
スポット溶接をうまく行う要素として①電流設定値②溶接時間③押し当てる圧力がある。パラメータのいずれかがうまくいかないと写真 3 1のように溶接どころか材料そのものを溶かしてしまうこともある。材料を押し当てる圧力も割と重要なパラメータであることが判った。
4. 失敗事例
4.1 試作機1
4.1.1 回路図
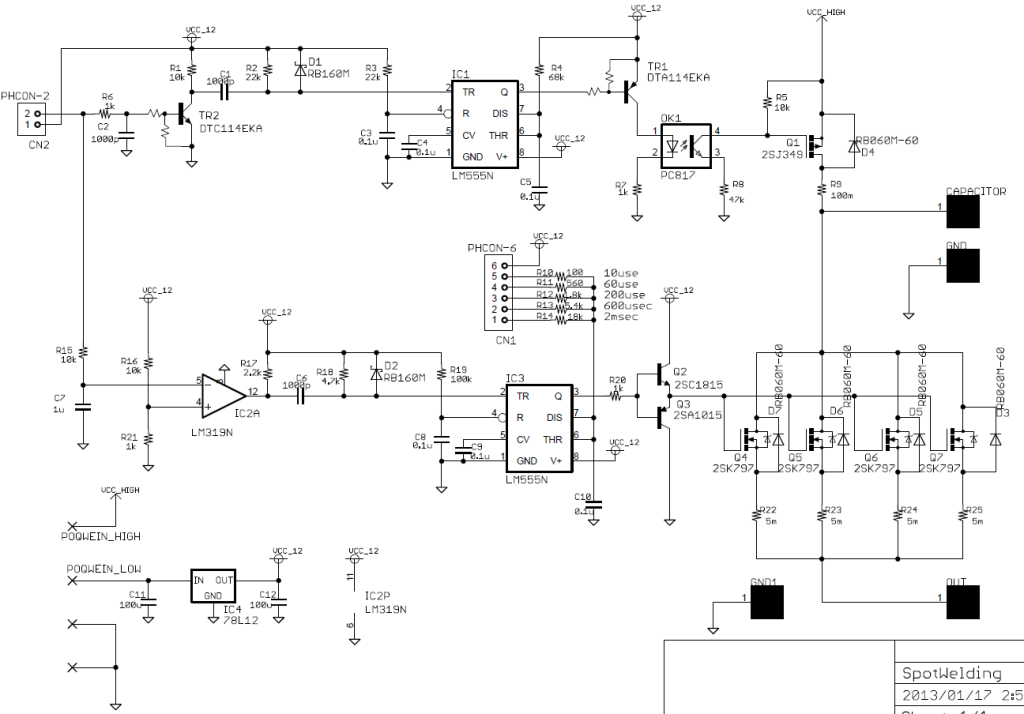
最初はコンパクトにまとめようとしてFETドライバー部も入れて1枚基板とした。
この後の評価試験においてFETが少なすぎることやNch-FETの使用方法が間違っていることが判明し、再度基板の設計のやり直しとなった。(;´_`;)
4.1.2 大きなミス
最初使用したFETが2SK797。VGSS=±20Vであり図 4.1‑2のAのように接続すると電源が20V以上になるときこのVGSSの定格を超えてしまうようで頻繁に壊れた。最初何が原因か判らなかったがよく見直してみると負荷を挿入する位置が間違っていることが判明。図 4.1‑2のBのような接続であればVGSSが20Vを超えることはない。
ちなみにゲートスイッチ電圧はFETのON電圧は4Vだが12Vでおこなっていた。
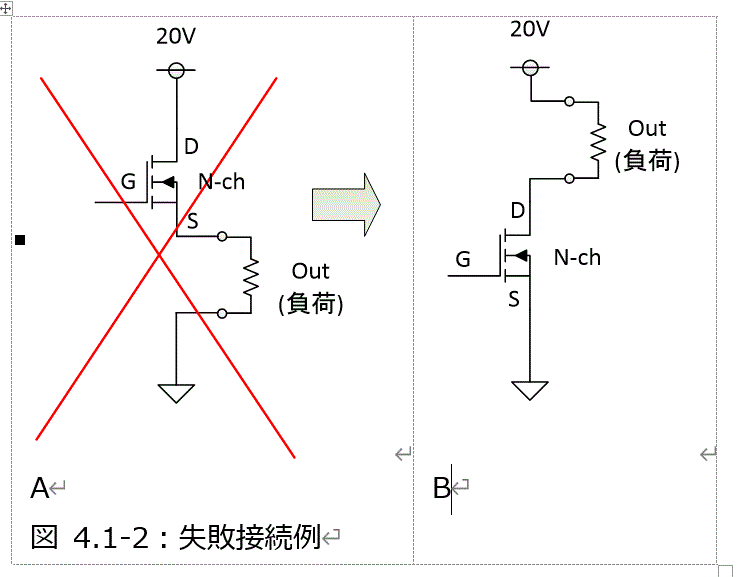
CNCを使用して初めて切削したガラエポ両面基板。今更ではあるが、かなりパターン設計が雑ですね。(;´_`;
4.2 試作機2
4.2.1 電流スイッチFET
余っていたNch-FET(写真 4‑1)のON抵抗を測定してみたところ数十mΩだったのでこれを使用してみたところ、一発で壊れた。やはりはっきりした仕様がないものは今回大電流のON/OFFのような目的がはっきりしたところには使えない。おそらく許容電流よりもVDS耐圧が高いFETだったのかもしれない・・┐(´-`;)┌
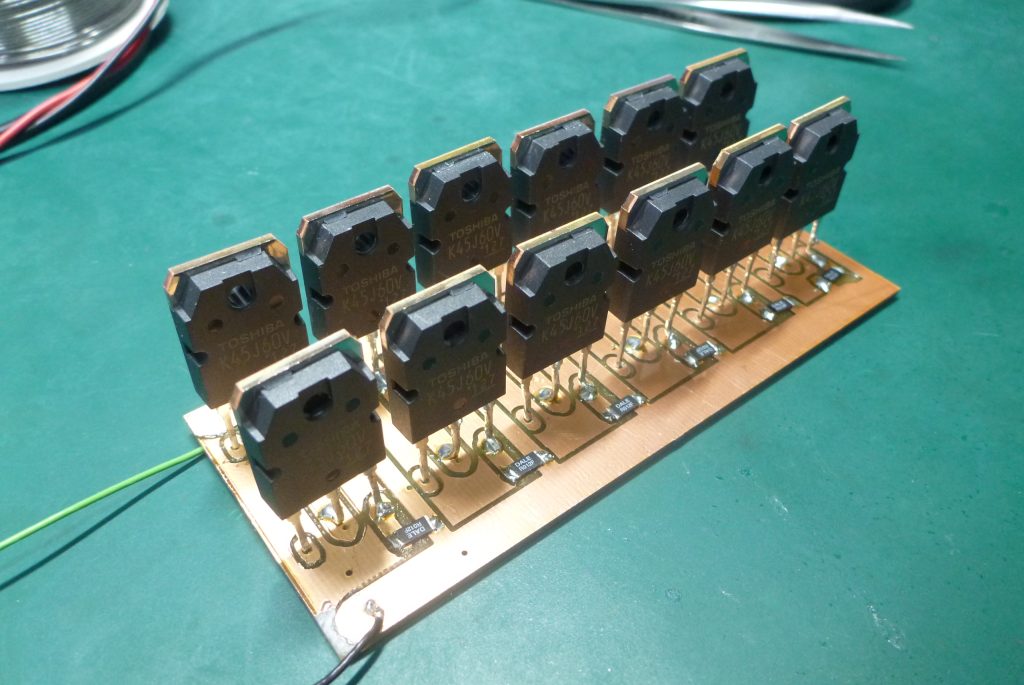
このFETドライブ基板も後で使用するFETのパッケージと異なったため、この基板も設計し直しとなった。ただし制御基板と分割していたためドライブ基板だけやり直しするだけでよかった。\(^O^)/
ここで学んだことは大電流を扱う場合、少しの失敗ですぐにデバイスが壊れることである。
また、FETをパラで使用した場合、ON抵抗のばらつきで小さいモノに負担が増し、劣化が激しくなる。
この対策としてそれぞれのFETに保護用の抵抗を挿入する必要がある。この抵抗により大きな電流が流れるFETには電流帰還が働き電流を制限する。今回の使用目的の場合、なるべくこのドライブ回路の合成抵抗を小さくする必要もあるため、FETそのもののON抵抗が極力小さい必要がある。
4.3 導体抵抗問題
配線の抵抗値を測定してみた。
+側:コンデンサの端子から銅棒までの抵抗値約5mΩ
-側:FETスイッチ基板から銅棒までの抵抗値約4mΩ
仮に100Aの電流を流すとするとV=I2×Rより1002×0.009=90Vとなる。
元の電圧はそこまでないので、結局電圧降下により100Aは流せていないことになる。
少なくとも9mΩを1mΩくらいにする施策が必要かもしれない。
使用側の対策として電圧を上げることで、電圧降下分の補える効果も期待できる。